The origin of bread in 3D printing
At Rebread, we are exploring ways to use surplus bread as a raw material to create new, sustainable products. We knew about the possibilities of using biopolymers in 3D printing, like corn starch or sugar beet. So why not harness surplus bakery or bread side streams?
"Any way to save bread from becoming waste and keep it in a closed production cycle is the right way. We are looking for solutions that we could apply globally. Our friend mentioned the high-tech company Sygnis, which could be open to such a collaboration",
– comments Bartlomiej Rak, CEO of Rebread.
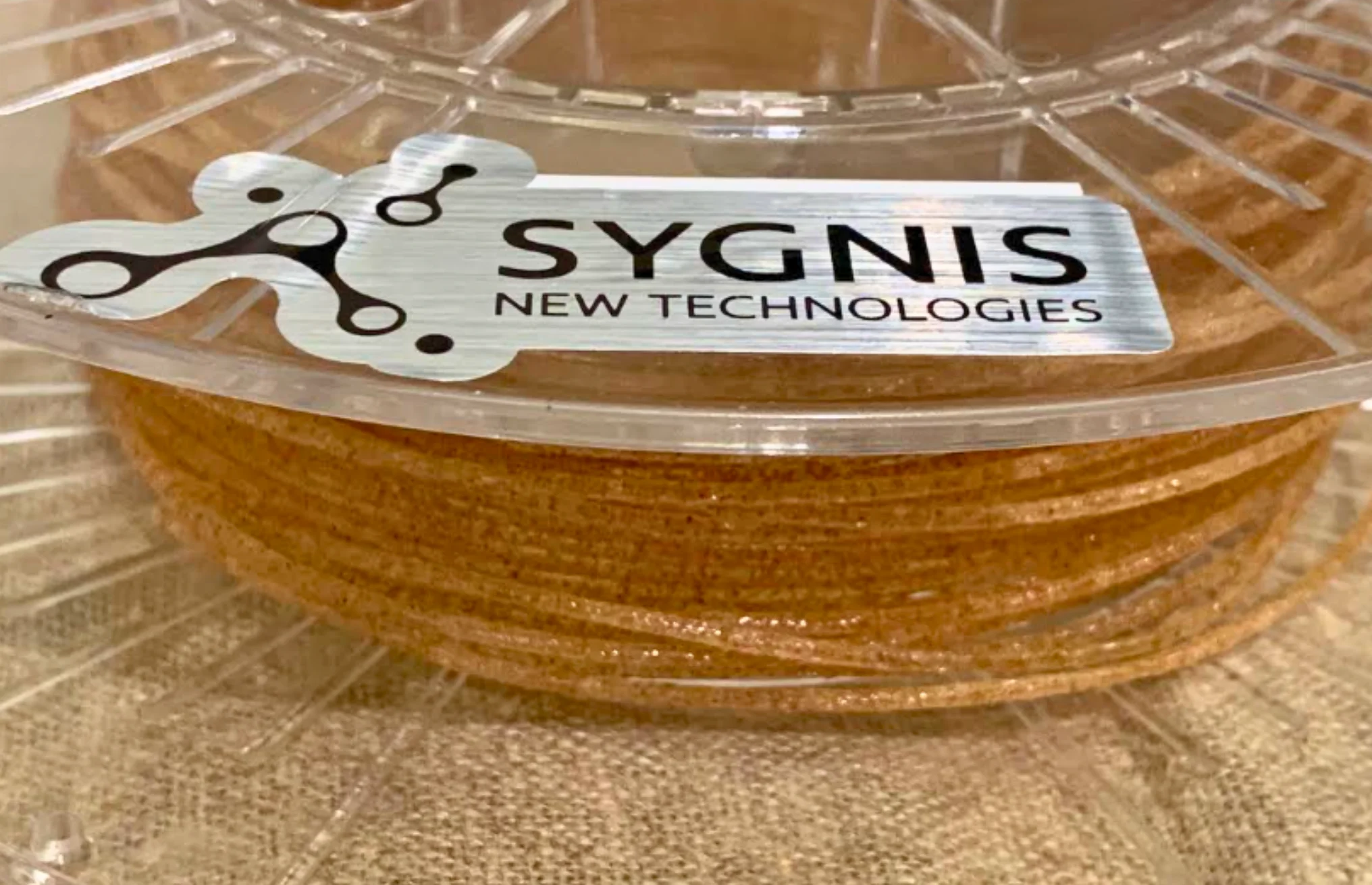
Collaboration sparks innovation
Cooperation is essential in finding solutions for bread waste management. Andrzej Burgs, CEO of Sygnis S.A., reacted to the idea with great enthusiasm. He quickly declared his willingness to cooperate and test the potential for reusing unsold bread in the production of 3D printing material.
We delivered a bag of surplus bread to Sygnis’ machine park, and work began to explore trends in bread waste utilisation – creating a filament using biodegradable PLA (polylactide) plastic combined with bread.
The role of 3devo machines in success
The work on this bread waste solution would not have been possible without the machines of Dutch company 3devo, which allow for trials on innovative materials like milled bread. Their mission is to promote sustainable 3D printing practices by closing material loops. This means endless possibilities for bakery waste valorisation.
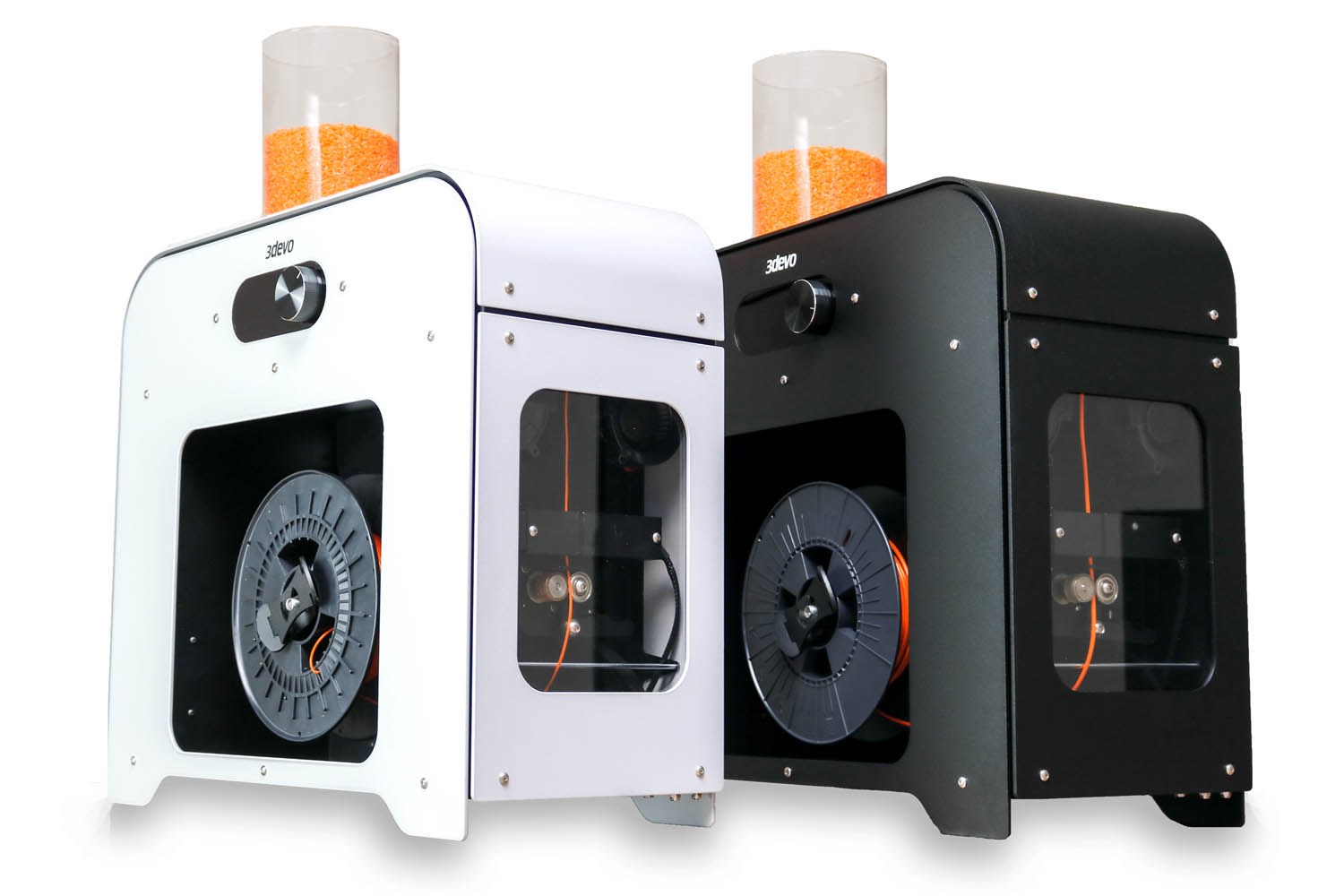
Joanna Wądołowska-Frej, an engineer in Sygnis's R&D department, shares:
"We are working with 3devo because our visions of the future are aligned. We want to take care of the environment by promoting green technologies that bring us closer to closing the waste cycle. We are committed to developing the recycling potential of 3D printing materials not only within our machine park, but also in industrial and research environments. Thanks to our Dutch partner's solutions, research into new materials is easier to carry out and the entire ecosystem of equipment takes up little space, offering endless possibilities in return."
How the processing works
We can grind the black bread easily because it is free of water. We then mix it with polymer granules at a ratio of 1:9 and can successfully extrude it using the 3devo Composer 450 machine.
After grinding bread, the pre-prepared mixture of granulate and the bread is poured into the hopper, or funnel. The mixture is fed into an auger/screw with a geometry that facilitates homogeneous mixing of the polymer and additive. This means that both components are evenly, uniformly mixed.
In order to achieve complete melting of the polymer, the auger/screw guides the material through four heating zones, each of which has a suitable temperature set independently. This can be neither too high nor too low. This allows us to change the state of aggregation of the material at the appropriate rate without changing the chemical composition of the mixture.
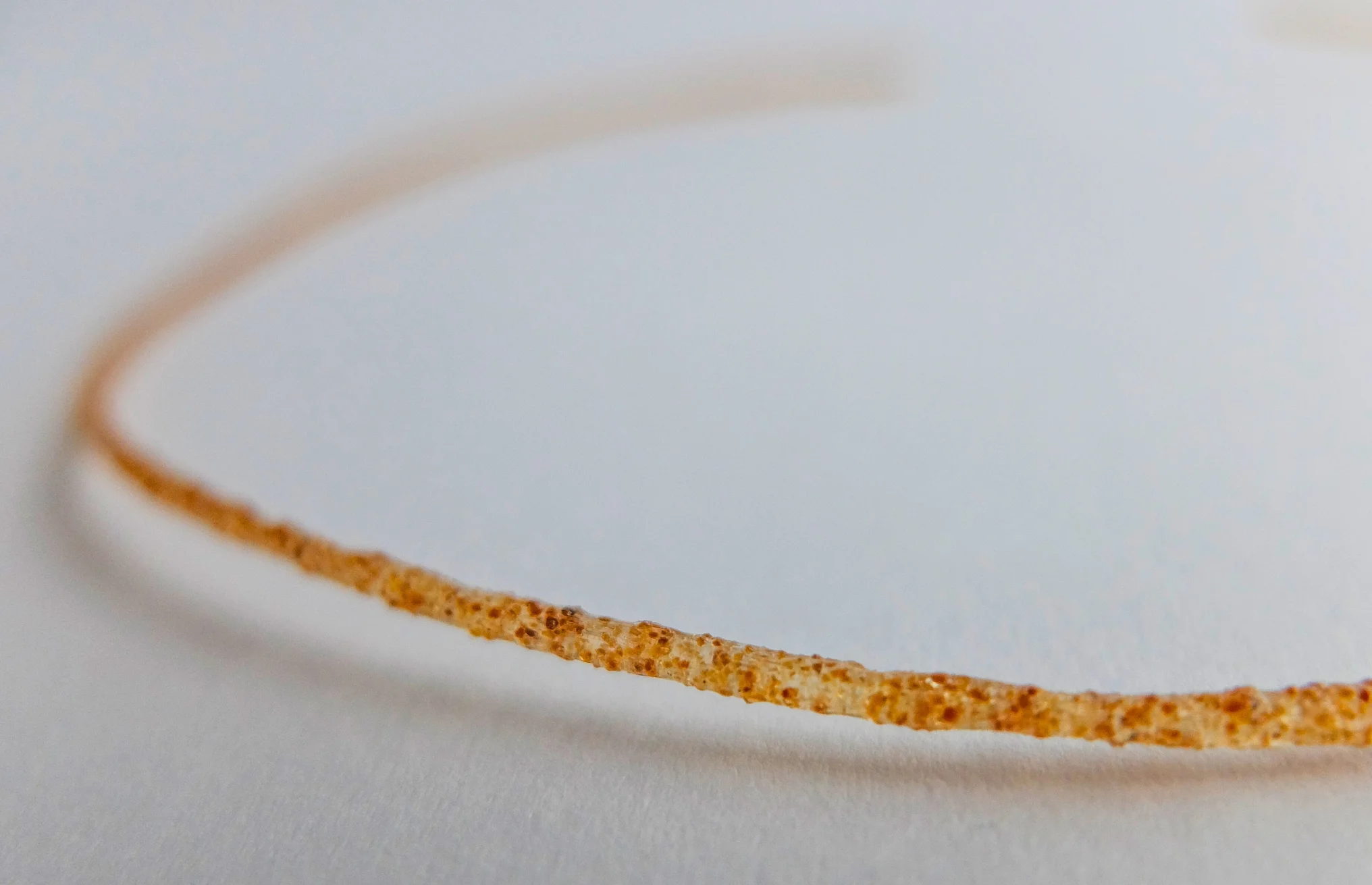
The extruder at the end of the screw/screw has a nozzle with a diameter of 3mm, from which the prefabricated filament flows stably. Next to it is a sensor that tests the diameter of the filament. It indicates whether the resulting material has a constant diameter. In addition, the extruder is able to automatically adjust the tensile force to maintain the diameter set by the user.
What does this mean? It means that the machine is able to maintain its own operating parameters to create the 3D printing filament again!
What we achieved
Through this collaboration, Rebread and Sygnis created a 3D printing filament composed of 90% PLA and 10% surplus bread. This filament supports sustainable innovations while addressing bakery waste.
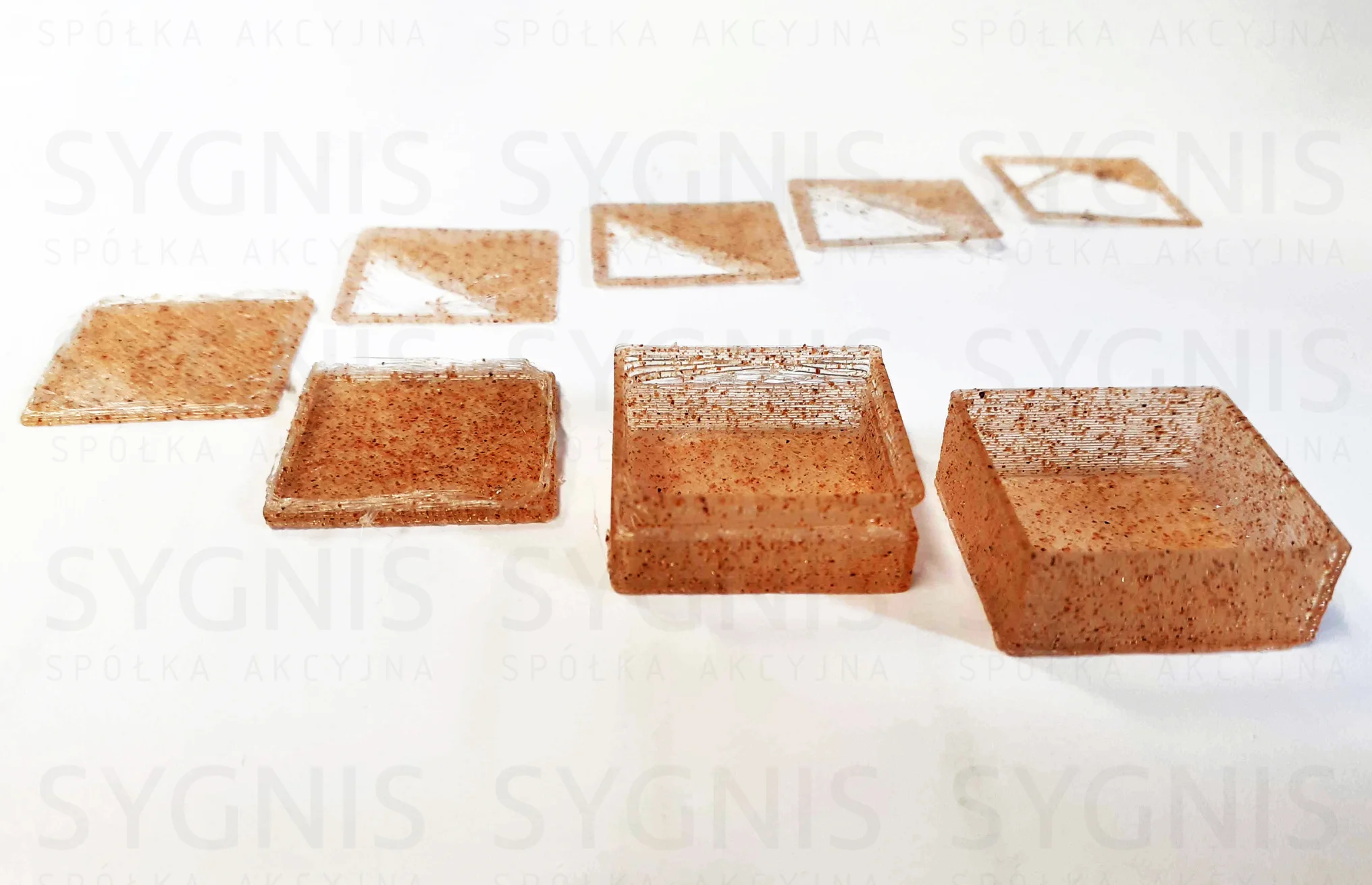
Despite challenges in perfecting the polymer blend, 3devo’s ready-made material profiles facilitated a smooth development process.
"The most difficult part was preparing the right polymer blend with black bread. The whole process went quite smoothly, as 3devo provides ready-made material profiles for the most popular thermoplastics for 3D printing. They make it easy to work with new blends and experiment independently",
– comments Natalia Pawlowska, junior engineer in the R&D department of Sygnis S.A.
More innovations to come
In Poland, approximately 2 million tonnes of bread are wasted annually, highlighting both a significant challenge and an opportunity for innovative bread waste solutions. Unsold bread demonstrates enormous potential as a versatile raw material for various industries.
As explains Bartlomiej Rak,
"Our aim is to inspire others and encourage collaboration between different industries that will work together towards not wasting food and taking care of the closed loop in business. Our project with Sygnis brilliantly shows how waste in the food industry can become a raw material in a completely different industry."
Read more about our anti-waste solutions!